Introduction
In the era of Industry 4.0, industrial automation is evolving rapidly. Engineers now face the challenge of selecting the right platforms and programming languages to meet new technological demands. This post explores how to navigate these choices effectively.
The Role of Programmable Logic Controllers (PLCs)
PLCs are integral to industrial automation. Known for their reliability and robustness, they are designed to operate in challenging environments. PLCs are traditionally programmed using languages like:
- STL (Statement List): A low-level language for precise control.
- FBD (Function Block Diagram): Visual programming for process control.
- Ladder Logic: Resembling electrical relay logic diagrams, it’s intuitive for engineers familiar with traditional control systems.
These languages enable precise and efficient control of machinery and automation lines, forming the backbone of many industrial processes.
Modern Demands of Industry 4.0
The shift towards Industry 4.0 introduces complex requirements:
- Interconnectivity: Machines and systems need seamless communication.
- Advanced Data Processing: Handling and analyzing large data sets in real-time.
- Flexible Control Systems: Rapid adaptation to changing production needs.
To address these challenges, engineers are increasingly turning to higher-level programming languages.
Python: A Versatile Solution
Python has emerged as a powerful tool in the industrial sector. Its strengths include:
- Ease of Use: Python’s simple syntax makes it accessible to engineers.
- Extensive Libraries: A wide range of libraries supports diverse applications.
- Integration Capabilities: Python easily interfaces with other systems and technologies.
Platforms such as Raspberry Pi and industrial variants like Kunbus enable Python to operate in industrial environments, offering a flexible alternative to traditional PLCs.
Key Python Libraries for Automation
Python offers several libraries tailored for automation tasks, including:
- PyMODBUS: Facilitates communication with Modbus devices, commonly used in industrial control systems.
- pySerial: Manages serial communication, essential for connecting various hardware components.
- OpenOPC: Provides seamless integration with OPC servers, crucial for process control and data exchange.
- Twisted: Supports network programming, enabling real-time data transmission.
- Robot Framework: A versatile tool for test automation, ensuring systems run smoothly and efficiently.
Combining PLCs and Python
A hybrid approach leverages the strengths of both PLCs and Python:
- Ladder Logic: Handles low-level control, interfacing directly with I/O devices.
- Python: Manages higher-level control, data analysis, and communication with external systems.
This combination allows engineers to create robust and adaptable automation solutions.
OPC and System Integration
OPC servers play a critical role in modern automation by:
- Enhancing Integration: Bridging the gap between industrial processes and higher-level software like MES (Manufacturing Execution Systems) and ERP (Enterprise Resource Planning).
- Enabling Monitoring: Providing real-time insights into operations.
- Ensuring Security: A strong emphasis on network security and data management is essential.
These systems require robust Ethernet networks or cloud-based infrastructures, fortified with comprehensive security measures.
Conclusion
The integration of PLCs with modern programming languages like Python offers a dynamic approach to industrial automation. By selecting the right tools, engineers can design systems that are efficient and adaptable to the evolving demands of Industry 4.0. This strategy ensures that automation remains at the forefront of technological innovation, driving productivity and efficiency across industries.
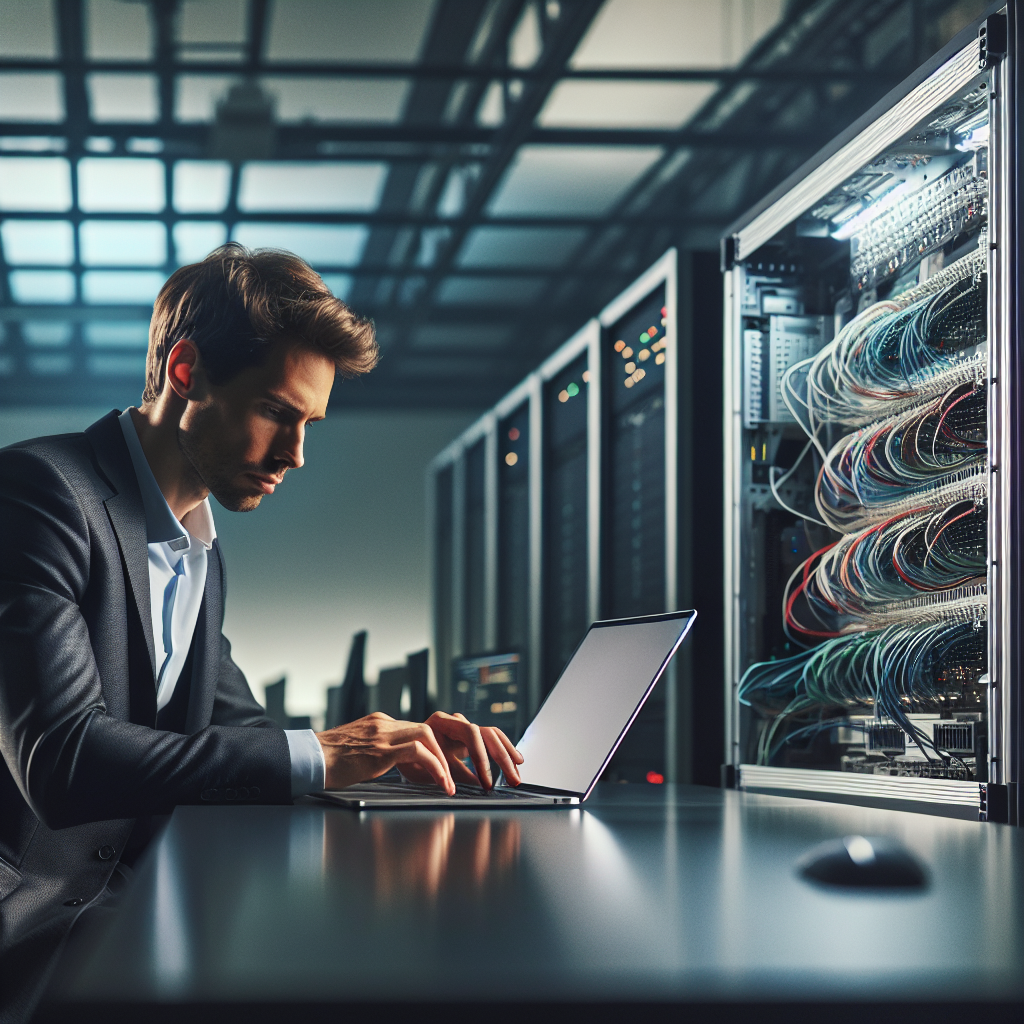
Leave a Reply