In recent years, 3D printing has emerged as a revolutionary force in manufacturing, offering several key advantages over traditional machining methods. One of the most notable benefits is the ability to create complex shapes and geometries that would be difficult or impossible with conventional techniques. 3D printing eliminates the need for specialized tools for every new design, allowing manufacturers to swiftly move from concept to production. This is particularly valuable for producing prototypes, new products, and low-volume series, significantly shortening the time to market.
Additionally, 3D printing optimizes material usage. Unlike subtractive manufacturing, where material is carved away, additive manufacturing builds parts layer by layer, reducing waste. This makes it an appealing option for sustainable production practices, aligning with global trends toward minimizing environmental impact.
The Challenges: Speed and Material Availability
However, despite its promise, 3D printing faces several challenges. One key limitation is the relatively slow production speed for single pieces. While it’s excellent for one-off prototypes or small batches, scaling up production for mass manufacturing can still be more time-consuming compared to traditional methods.
Material availability is another hurdle. Although 3D printing theoretically supports a wide range of materials, commercially available options are still limited. The majority of 3D printers in use today rely on plastic, and while there has been significant interest in printing with metals, ceramics, and even glass, these materials are not as widely accessible. Metal 3D printers, in particular, tend to be far more expensive than their plastic counterparts.
The industry is slowly expanding its material options, and there are promising developments in glass and ceramic 3D printing. However, these are still in the early stages of commercial availability, making it a challenge for companies looking to adopt these materials in their processes.
The Skills Gap
For many companies, particularly smaller businesses, in-house expertise remains a barrier. 3D printing requires specific knowledge and experience, and as the technology evolves, staying current on the latest advancements can be a challenge. Training staff and integrating 3D printing into existing workflows can involve steep learning curves.
Conclusion
As one of the pillar technologies in Industry 4.0, 3D printing is making steady progress and continues to evolve. Despite the challenges of speed, material availability, and technical expertise, the technology holds immense potential for transforming how we produce goods. MilovanInnovation will continue to track new developments and trends in 3D printing, ensuring you stay informed about this rapidly advancing field.
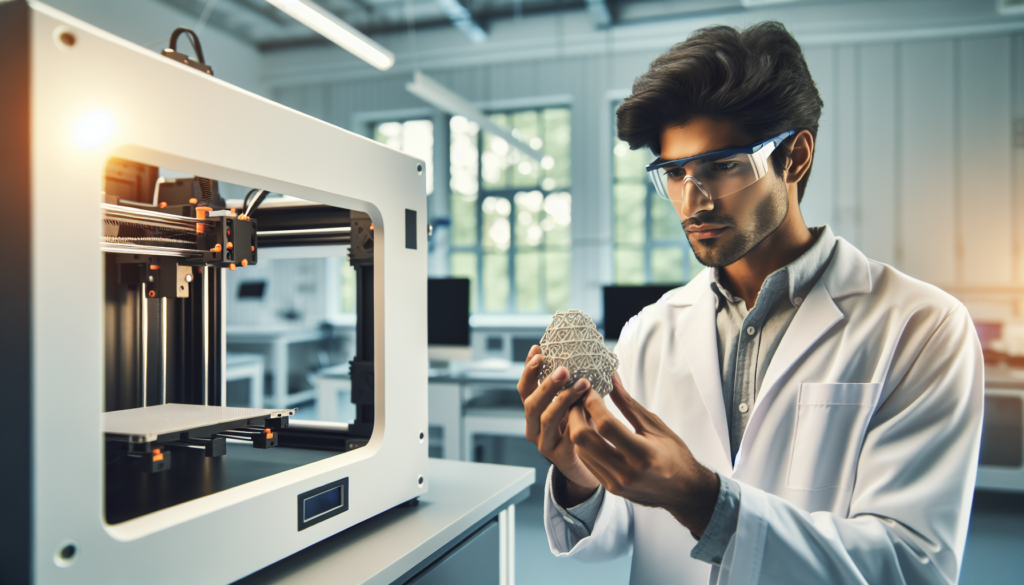
Leave a Reply